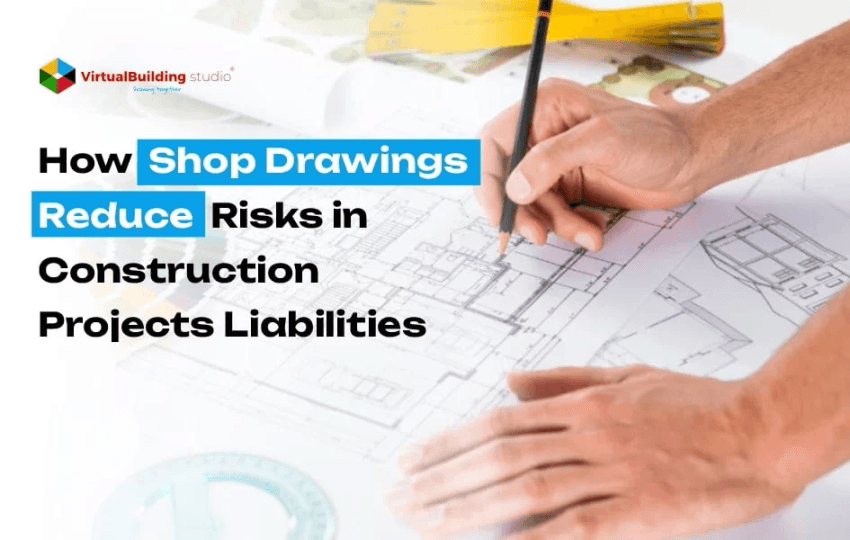
Drawings are an integral part of the building-making process and architectural construction documentation. MEP Shop Drawings are created by professionals to ensure seamless, safe, and timely completion of the construction process.
These drawings are created as per the design intent of the architect. The shop drawings are detailed and provide precise instructions for all perceptible structures, including steel beams, electrical wiring, HVAC systems, and plumbing equipment.
Challenges Faced Without Accurate Shop Drawings
Project Setbacks:
Enigmatic directions lead to delays in fabrication, installation, and assembly that hamper the project timelines. The project setbacks might result in poor construction quality and work discrepancies.
Budget Overruns:
Disrupted work schedules and unclarity of design leads to rework on construction sites. Rework and project delays cause budget overruns due to material wastage, labor, extended time, and potential penalties.
Miscommunication:
Multiple team collaboration and managing ample project data might result in incorrect or unreliable transfer of information between the stakeholders. The miscommunication of information causes project delays and cost overruns.
Coordination Issues:
Scattered MEP shop drawings impede coordination and discourse between various disciplines, fueling conflicts during on-site construction. A messy workflow lacking coordination among team members makes it difficult to execute construction work and deliver quality results to the client.
Quality Problems:
The absence of specific project information jeopardizes overall work quality. The quality issue leads to below-average construction and safety problems.
Legalities and Client Dissatisfaction:
Inconsistent work and incomplete shop drawings result in illegal problems between project teams. Construction projects executed with inaccuracies, clashes, delays, rework, and low-quality lead to client dissatisfaction.
Types of Shop Drawings
Construction shop drawings deliver precise, scaled, detailed, and specialized information about multiple elements. The different types of drawings facilitate precise construction and ensure that building components comply with design, codes, regulations, and safety protocols.
Architectural Shop Drawings
Architectural shop drawings are detailed blueprints developed by architects to offer specifications of construction elements.
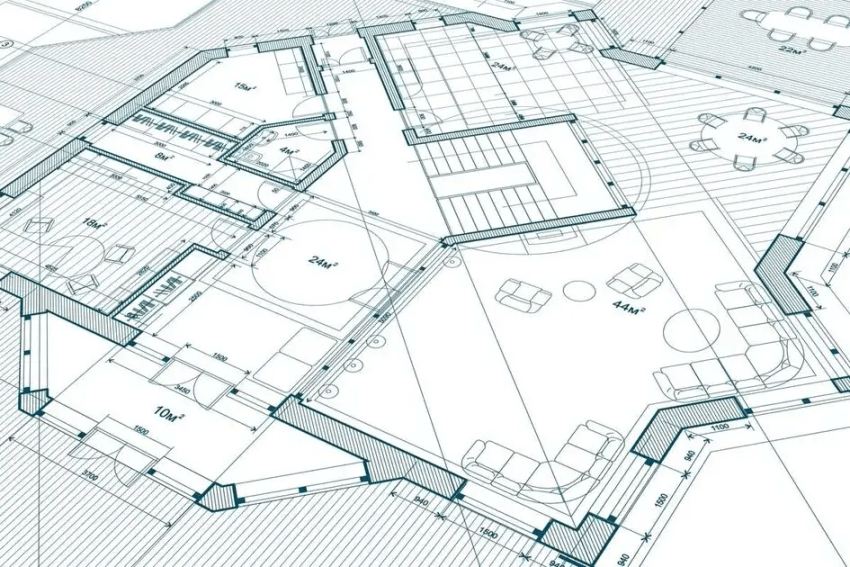
The builders and contractors seek guidance from these drawings for accurate information about the architectural design and to achieve construction outcomes aligned with the architect’s vision.
Structural Shop Drawings
Structural shop drawings are explicit blueprints depicting important components of the building framework. These drawings are generated by structural engineers to provide precise plans of concrete building elements including columns, beams, and connections.
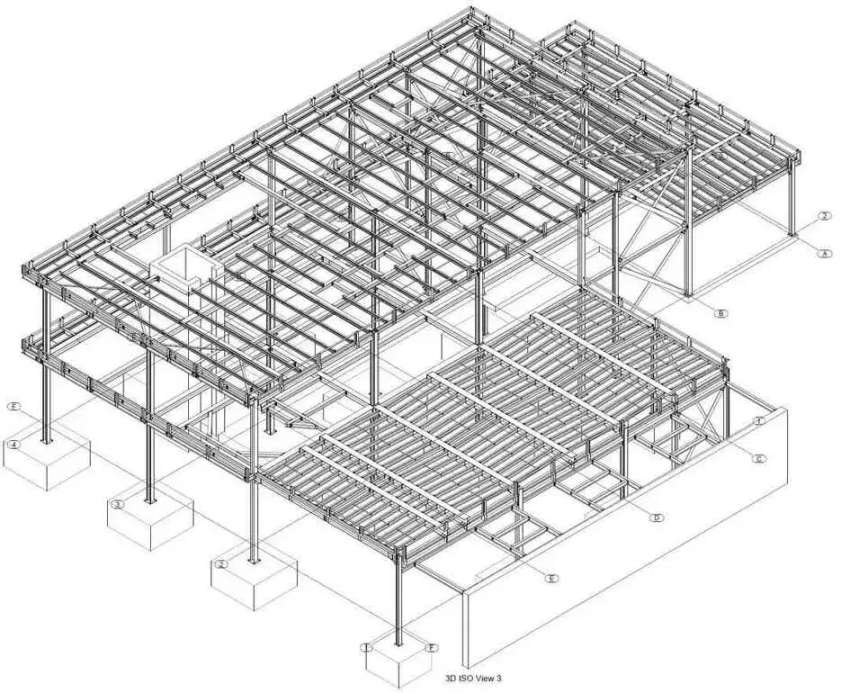
These guides offer essential guidance for accurate load-bearing construction work, ensuring structural integrity.
MEP Shop Drawings
MEP shop drawings emphasize mechanical, electrical, and plumbing systems. These drawings entail specifications about HVAC systems, electrical wirings, ductwork, and plumbing fixtures for a seamless infrastructural experience.
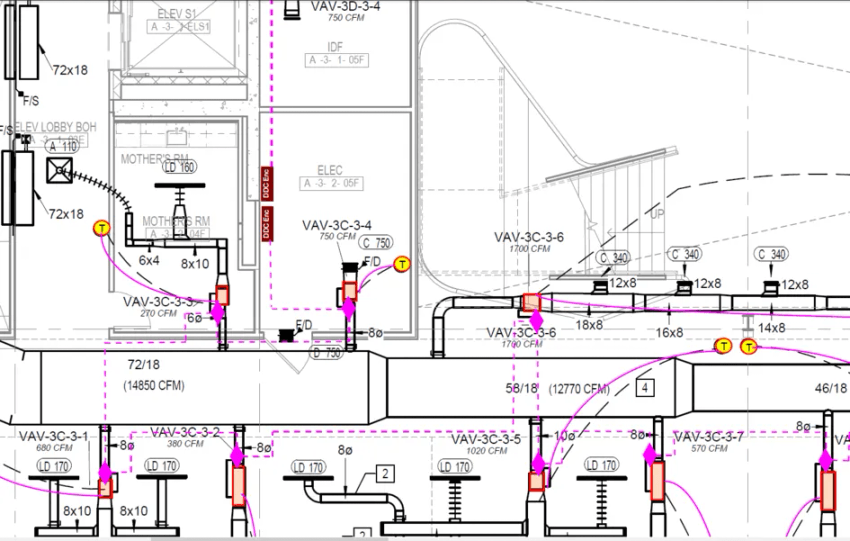
Built by MEP engineers, these shop drawings play a vital role in facilitating smooth coordination between various building systems.
How do Shop Drawings Ensure Synergy with Design Intent?
Shop drawings play a significant role in conveying the design intent to the stakeholders for accurate construction work.
These drawings offer detailed and customized project layouts developed by contractors, fabricators, and manufacturers to bridge the gap between conceptual design and actual implementation.
The design clarity allows the client to better visualize the final structure. Shop drawings ensure the synergy of design intent with meticulous detailing, elaborative dimensioning, specifics about construction techniques, and material details.
Importance of Shop drawings in construction
Accurate and precise data provides a unified understanding of design to the stakeholders and establishes a smooth relationship between them. It leads to design integrity, enhanced efficiency, and controlled construction costs. Here are a few ways to elaborate on the importance of shop drawings in construction:
Compliance with Building Codes and Standards
Construction in compliance with building codes and regulations helps in reducing risks and errors in architectural projects. Shop drawings are elaborative blueprints developed by stakeholders to depict accurate material specifications and techniques.
Thorough assessment supports architects and ensures compliance of proposed plans with standards and safety codes. The project team can identify potential risks and their appropriate solutions before actual construction begins on site. This helps in mitigating expensive problems, ensuring the project’s regulatory compliance, and lowering the probability of inefficient construction.
Identifying and Mitigating Potential Conflicts and Errors
Shop drawings minimize the chances of conflicts and errors during construction work through the identification and mitigation of any possible issues. Accurate and detailed shop drawings act as a connecting passage between architectural plans and execution on-site.
Intense audits of shop drawings eliminate potential clashes and ambiguities in the pre-construction stage. These preemptive methods ensure swift construction and improve project risk management.
Eliminating Miscommunication and Enhancing Collaboration
Accurate shop drawings Services offer risk reduction to a great extent, eliminating miscommunication among project stakeholders.
Explicit and detailed shop drawings promote project-wide collaboration, improving understanding of the design intent and resolving potential issues. It fosters project growth, improves project management, and ensures minimal setbacks.
Liabilities in Construction Projects
A serious construction threat for contractors, project owners, and designers is ignoring building standards, codes, and regulatory norms at the time of building construction. Common liabilities include preventing workplace mishaps, project delays, and building defects.
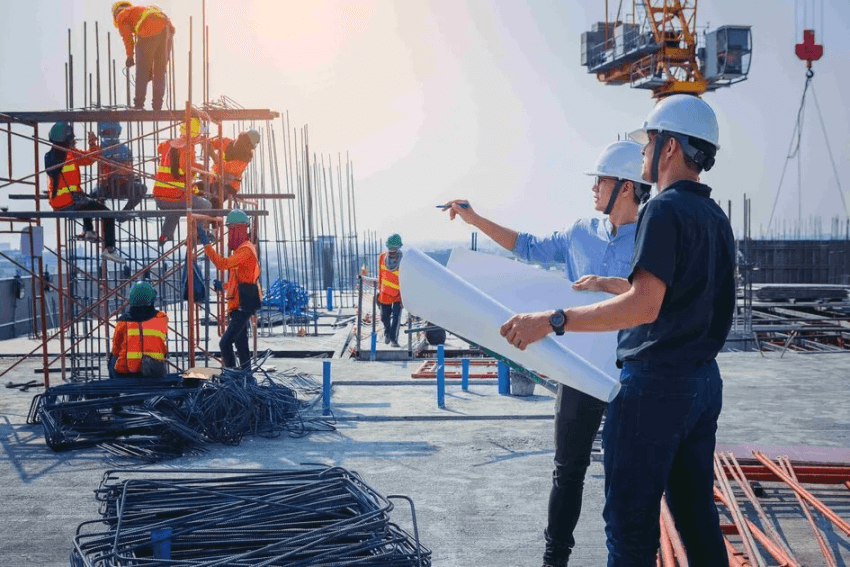
Contractors hold responsibility for below-average work or time overruns resulting in legal issues. Adhering to regulations and ensuring build quality is the liability of the project owners. Rigorous contracts and safety protocols should be implemented to protect every party involved in the construction process.
Some other construction project-related liabilities are:
Financial Consequences of Construction Liabilities
Non-adherence to construction codes and regulations has significant financial implications. The project team has to face cost-based delays, safety breaches, and construction defects leading to hefty monetary punishments and legal battles adding to the financial strain.
Mitigating construction defects and errors requires additional expenses, emphasizing the need for conscious regulatory compliance, extensive QC, and complete risk management.
Legal Consequences of Design Errors and Discrepancies
Design errors and discrepancies lead to significant legal issues causing budget overruns, structural problems, and project delays that expose the stakeholders to legal liabilities. Architects and engineers are held accountable for professional failures, while contractors deal with contract breaches for flawed designs.
Compliance with global construction standards and proactive risk management is important to wave off legal issues and maintain project performance.
Role of Shop Drawings in Curtailing Liabilities
As it is imperative to curtail construction liabilities from AEC projects, adapting shop drawings for design execution by project stakeholders can be the most appropriate option. The role of shop drawings in eliminating these liabilities is as follows:
Prevent Design Errors
Shop drawings help in managing construction liabilities by providing preemptive error detection and the required solutions. The drawings entail construction details and specifications that ensure the intended vision aligns with the proposed design. The explicit design details eliminate the scope of design errors and defects during on-site construction.
Ensuring Compliance with Documentation
Developing accurate and data-infused shop drawings leads to the mitigation of construction liabilities and sets a benchmark to achieve compliance with architectural standards. These drawings provide a crisp depiction of project execution through the illustration of building materials along with architectural, structural, and MEP dimensions.
Shop drawings ensure complete documentation of the project, safeguard liabilities, and thorough analysis lowers the risk of discrepancies.
Resolving Disputes and Legal Issues
Contractors can leverage clear project documentation with the presence of every minute detail and specification within shop drawings.
These drawings significantly minimize conflicts and legal issues through visual representation of the proposed layouts. The preparation of shop drawings eliminates legal liabilities, enhances transparency, and ensures fair resolution for the protection of all parties involved in the project.
Conclusion
The importance of shop drawings in construction projects is understated as the accuracy, extensive detailing, and compliance with standards significantly lower liabilities and risks.
Shop drawings act as a communication tool for various project stakeholders by illustrating design specifics, eliminating misunderstandings, and increasing the efficiency of the project.
The AEC professionals should embrace the benefits of MEP Shop Drawings for construction projects, enhancing the standards of building construction and promoting design excellence.