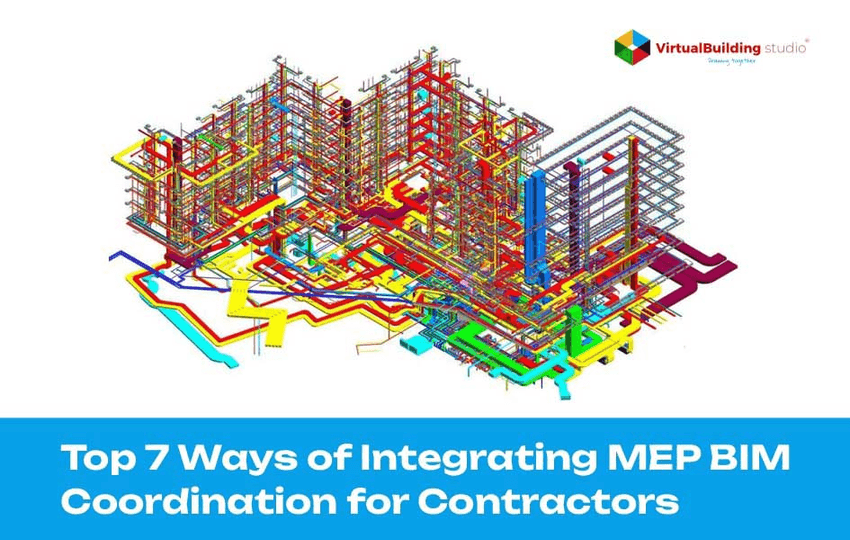
A building is a comprehensive model constituting several elements combined to cater to different needs and offer maximum functionality. Mechanical, Electrical, and Plumbing (MEP) systems are the most complicated elements running throughout the structure, creating a congenial environment for the occupants.
An efficiently designed MEP system provides a sustainable environment to the occupants, facilitating heating, thermal, and visual comfort. Building Information Modeling (BIM) is increasingly applied to MEP services in the construction industry.
MEP BIM coordination is becoming the new normal with 2D software becoming obsolete due to the difficulty of understanding 2D drawings.
The 3D MEP drawings are easy to visualize and communicate for installing these systems on the construction site. Innovative technology and suitable management methods together lead to an improvised workflow, coordinated design, and reduced conflict on construction sites.
It is technically more challenging to coordinate MEP services with BIM, as compared to other building services. The use of BIM over 2D drafting software requires thorough research to reduce manual labor and improve clash detection, and machine learning to accelerate the design process. Coordinating these services with MEP shop drawings saves more than 50% of the project duration invested otherwise.
Challenges with Traditional MEP Coordination Systems
The traditionally used 2D methods for MEP coordination are costly, time-consuming, and inefficient at clash detection. Here are some of the challenges faced by MEP contractors using traditional methods:
- Visualization of spaces becomes a tedious job, making it difficult to convey the design requirements and leading to a successful work completion.
- MEP coordination in congested spaces leads to conflicts and design clashes.
- Unexpected changes become difficult to accommodate at later stages, resulting in expensive reworking.
- Problem resolution becomes a common concern due to interference from every team member leading to more chaos and unresolved issues.
- Lack of automation for clash detection leads to time-consuming sequential tasks.
- Decentralized design responsibility is another challenge to combat with manual MEP coordination.
- The project team provides inefficient pre-construction design reviews due to unclear drawings and specifications.
Benefits of Adopting MEP BIM Coordination for Construction Process
MEP BIM services depict the digital representation of a building’s mechanical, electrical, and plumbing systems as a comprehensive 3D model. This technological development brings multiple benefits to the industry:
Automated BIM Clash Detection
MEP systems involve the distribution of various elements such as ductwork, plumbing water pipes, electrical equipment, VAV boxes, and more, which leads to the complexity of the construction process. The various conflicts in MEP coordination pertain to these tricky system layouts.
MEP BIM Coordination automates coordination and clash detection by identifying hard clashes, soft clashes, and workflow interferences at an early stage.
A large number of hours invested in the manual process can be saved using BIM clash detection. The automated process simplifies the analysis and installation of the complex MEP systems.
Easy 3D Visualization and Resolution of Clashes
3D visualization generates a three-dimensional view of the entire building during the pre-construction stage, allowing MEP contractors to analyze any design clashes within a coordinated BIM model. The detailed views of interstitial spaces, sheer walls, firewalls, and corridors help the contractors in examining the exact available space.
This information allows efficient accommodation of MEP systems without any physical interference. The MEP shop drawings facilitate the mitigation of construction delays caused due to rework on site by devising alternative solutions to issues.
Stakeholders Function on the Same Page
MEP coordination and clash-free installation is functionally impossible without various disciplines working in sync with each other. A 3D coordinated MEP BIM model becomes a one-stop reference for all the different teams with all data embedded into one model.
This transparency and efficient working model allows the contractors and stakeholders to be on the same page. It provides better project clarity and leads towards a well-coordinated work affair.
Accuracy of Prefabricated Components
For renovation or building extension projects, it is a preferable choice to integrate MEP BIM coordination services. The BIM model of an existing building provides installation and layout details of the as-built including precise measurements of the ductwork.
The data facilitates chaos-free fabrication of components, seamless coordination, and smooth installation of the new MEP systems within the renovated structure.
Precise Site Planning and Construction Management
MEP shop drawings Services depict the infrastructural service placement and corresponding structural components. 4D BIM enables contractors to decide on material access paths and staging areas, and schedule material deliveries.
The workflow can be scheduled properly coordinating it with other stakeholders, facilitating accurate construction management and site planning. The induced accuracy and precision lead to a clash-free construction.
Smoother Site Execution with Zero Change Orders
MEP BIM coordination develops models with exact dimensions of MEP components and fixtures at the pre-construction stage. The model includes information about corresponding offsets, insulation details, and material specifications.
The availability of data leads to a seamless fabrication of the required parts of the MEP system accelerating the ductwork in a sequential manner and zero rework.
The pre-emptive changes in duct sizing, equipment, pipe rerouting, and splitting of the electrical ladder can easily be executed with the MEP BIM model.
Coherent Facility Management
Coordinated MEP BIM models provide details of access paths for building maintenance and repair throughout the life cycle of the building. The existing equipment such as air conditioners, electric wiring, and plumbing lines gets easier to access and repair.
It also allows vendors to safely reach these facilities with precise mapping of interstitial building space. The existing technology can be fixed and upgraded for energy conservation and reduction of running costs with MEP models.
Why is the Effective Management of MEP BIM Coordination Important?
BIM clash detection model comes with MEP fabrication drawings, MEP installation drawings, MEP shop drawings, as-built drawings, MEP construction drawings, spool drawings, facade drawings, and other required drawings.
The MEP BIM coordination services provide an output model inclusive of Architectural, structural, MEP models, and clash-free construction drawing sets.
Any discrepancies in the inputs from various stakeholders are rectified before any difficulty on site. The site execution is accelerated with clash-free drawing sets, leading to a time-bound solution.
Conclusion
MEP BIM coordination creates 3D models that enhance material planning and management, resolve conflicts, facilitate resources, and increase stakeholder collaboration. It is more than an interference check for the contractors as the automated processes eliminate any repetitive tasks and speed up workflows.The design and modeling process is completely digitized, combined with lean construction and agile processes, leading to a seamless MEP system installation.
The adoption of MEP BIM coordination has led to the drastic development of the architectural, engineering, and construction industries. The ability to visualize, create, and analyse detailed 3D MEP models is altering the way projects are designed, coordinated, and executed, adding value to the project.
With the progression of the AEC industry, embracing MEP BIM coordination is not just a competitive benefit but a requirement for staying relevant.