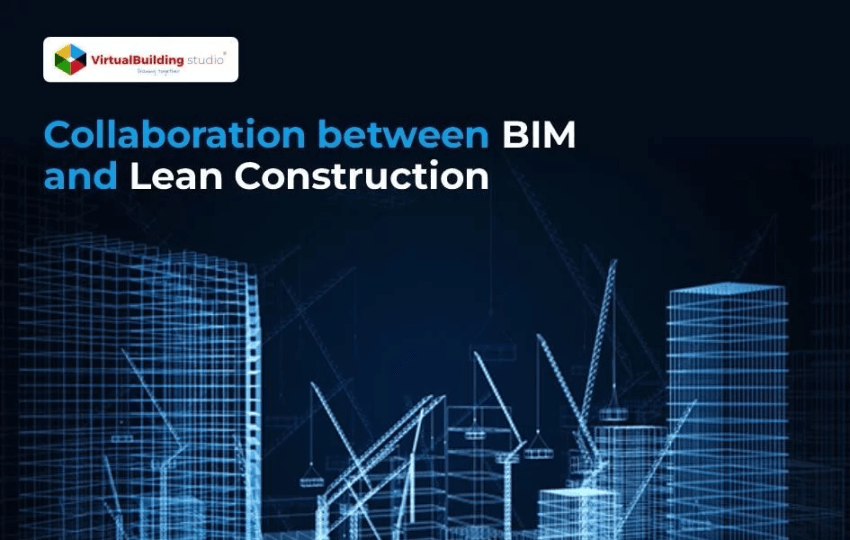
Lean construction is a new philosophy that has recently garnered a lot of attention from the AEC industry. Although this managerial philosophy emerged in the automobile industry, it has been spreading like wildfire all across. The objective of lean construction is to improve predictability in construction projects.
The idea is to identify and eliminate waste, improve productivity, reduce costs, and the overall time of the project, resulting in more efficient and safer outputs.
We, at the Virtual Building Studio, provide BIM Modeling Services to our clients through detailed engineering and quality control using our ample expertise ranging from design to on-site installation.
Our experts help clients in identifying and eliminating high-cost areas by re-designing MEPF services and resolving constructability issues.
Our team has been consistently working towards ensuring on-time project delivery and quality outputs. We have successfully handled a wide range of BIM projects with varying complexities for our clients in the USA, the UK, Singapore, Australia, and the UAE.
We are committed to providing our clients with the best of the opportunities that ensure their growth and success. We have been working towards establishing a firm foothold in the BIM industry, and our team of experts is leading the way.
Gregory A. Howell, one of the founders of this approach, has very rightly put it:
Our projects take a lot of time, cost too much, and kill many. The projects do not achieve the expected performance by the clients or the expected benefit by the designers, contractors, and suppliers.
These failures are often attributed to poor decisions made by project participants or unexpected circumstances. The experience applying lean principles to project management reveals deeper problems in the structure and practice of project management. Lean construction deals with these issues.
Now, we know that BIM provides tools to plan, design, construct, and manage projects more efficiently with an intelligent 3D-based modeling process.
Both BIM and lean construction are amongst the most talked-about construction approaches in the industry today. They have managed to increase the otherwise low-efficiency rates in the construction industry over recent years.
These new operations management concepts have been adopted to eliminate waste and add value to the final product. Although these two are quite different approaches, there are many synergies between them.
Because of several overlapping benefits, BIM and lean construction, when applied together, produce a synergistic effect and increase the efficiency rates multi-fold. Researchers have identified 56 different interactions between lean construction and BIM, 48 of which are constructive.
The following table by Allan Fred Onyango for the Department of Real Estate and Construction Management, Royal Institute of Technology, illustrates the interaction between BIM and lean:
Lean Construction | Intersection with BIM |
---|---|
Elimination of wastages (time, materials & effort) | Structural clash tests |
Design alternatives to select a most suitable design | |
Design alternatives to select a most suitable design | |
Customer Value (achieve requirements) | Visualization of solution that ensures a clear understanding of the model |
Analysis for best result | |
Understanding between client and supplier by use of 3D models and walk droughts | |
Reduced Cycle Times | Automated generation of changes and material schedules and quantities |
Provide accurate intonation to Prefabrication | |
Visualizing of workflow to check for process conflicts (teams and tasks) | |
Work Flow | Through making detailed schedules of tasks and materials delivery times |
Collaboration | Ability to work concurrently on same design solution by different teams |
We have several tools at our disposal for the effective implementation of lean. The most popular one is called the Last Planner System (LSP). As the name suggests, this system engages last planners- the people who are ultimately responsible for planning and executing the project.
LSP increases the success of construction activities by mitigating risks and other uncertainties that might pop up during the planning phase of the project.
To enhance the synergistic effect of lean and BIM, the collaboration should start early from the design phase so that it is well-planned, and the application during the production phase becomes easier.
In addition to LSP, some other integration tools include Kaizen, Set-Based Design, A3 Reporting, Target Value Design, Kanban, 5S, and Last Responsible Moment (LRM).
While it is true that the application of lean and BIM reduces costs, adds value, and increases the overall efficiency of the construction project, it is also important to note that an efficient leader needs to manage the flow at every stage of the building lifecycle. Also, a strong collaborative culture needs to be implemented between the contractors and the supply chain.
In conclusion, this relatively new philosophy is emerging as a collaborative process that yields higher efficiency rates and is taking the construction industry by storm.
The research is still underway, and they are investigating more ways to combine lean and BIM to integrate the construction process that yields more benefits.
They are still working out the challenges of implementing this kind of a process, but it seems that this collaboration is what is slowly transforming the construction industry today.